High-Speed Stimuli Generator for Engine Ignition systems
Abstract
WireFlow helped SEM (Svenska Elektromagneter) to develop an advanced, high performance and highly configurable Stimuli Generator (STIG) for up to 12 cylinder ignition systems. The system was built using National Instruments cRIO hardware and LabVIEW/LabVIEW-RT and LabVIEW-FPGA. The system can define stimulus for each cylinder in terms of ignition pulses, trigger pulses as well as engine speed and analog simulation data – everything relative to the start of an engine cycle (Crank Angle Degrees – CAD). The width of any digital pulse can be set in 0.01 CAD or in 0.1 ms steps resolution. Engine speed can be varied between 0-20 000 RPM, either as a predefined speed profile or manually when the system is running.

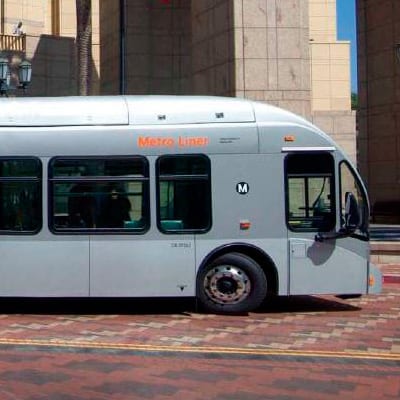
Challenges
SEM is one of the world’s leading producers of electronic ignition systems and engine control systems. SEM develops and produces high-end ignition systems for a variety of engines, ranging from one cylinder engines for chainsaw motors to big gas engine systems with 8 cylinders or more.
During development, it is important to be able to exactly control all parts of the ignition, like spark position and duration for each cylinder for a number engine cycles – representing a specific startup behavior or mimicking a faulty behavior.
One of the tricky parts is that spark duration can be given in CAD (0.01 degree resolution) or given as a fixed time (0.1 ms) depending on engine type, whereas spark position is always given as a position (CAD) in the engine cycle. In the figure to the left, a fixed configuration for four DO channels are shown for two different engine speeds.
Solution
Using LabVIEW and a high end cRIO from National Instruments™ WireFlow created a system that allows the technicians at SEM to select predefined engine cycles using a touch-screen. The user can also manually control all aspects of the ignition cycle, including position and duration of each ignition pulse as well as the reference pulse using different slider bars in the GUI. It is also possible to manually change the RPM value while maintaining the pulse characteristics, i.e. the position and duration regardless if it is given in time- or CAD-domain. The system consists of four main LabVIEW components,
- The FPGA
- The RT Controller
- The Runtime control GUI (pictured above)
- The Stimuli Configurator GUI
In the offline Stimuli Configurator, GUI technicians define a specific engine cycle with a unique speed profile. The profile is transferred to the cRIO as a TDMS file and played back using the Runtime Control GUI.
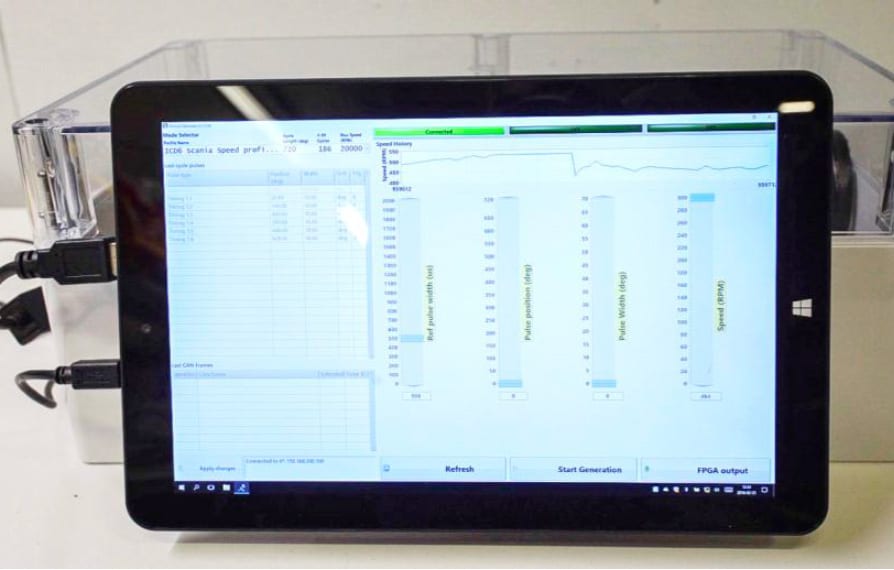